Have a TPO roof?
Are you dealing with multiple leaks, seams are losing adhesion, or have tiny pinholes?
If so, it’s time to do something with your roof.
Here’s what we’ll cover in this article:
- How can you tell your TPO roof’s life is almost over?
- What repair/restoration options do you have?
- How much does each repair/restoration option cost?
- What problems should you look out for?
And just so you’re aware, West Roofing Systems has been in commercial roofing since 1979. We’ve repaired, restored, or replaced hundreds of TPO roofs across the Eastern part of the US.
Each article written is reviewed by a commercial roofing specialist with more than 30 years of experience.
Let’s get started!
How can you tell your TPO roof’s life is almost over?
If you’re like most, what triggers you to look on the roof is a leak. If there are no leaks, the roof is out of sight, out of mind, and most people simply ignore it.
But if you have a leak, you most likely send a maintenance tech to see what’s going on above the area where it’s leaking inside.
Here are some signs that your TPO roof’s life is at its end:
Reason #1 – The seams are coming apart
Even if there’s a slight opening in your seams, every future gust of wind will separate those seams even further.
If the adhesion holding the seams together has worn down, has been damaged by UV rays, fasteners have backed out, the weld was installed too hot/cold, or any other reason, when the seams begin to lose adhesion is when the TPOs life is about over.
Reason #2 – Pinholes
Pinholes can happen because the adhesive that holds the seams together has been burnt away from UV rays. Pinholes can also happen from animal damage, small branches, nails that have been dropped and stepped on, etc.
Over time the membrane’s top surface wears down, fibers start showing, which makes it deteriorate a lot quicker; creating possible water entry opportunities.
Any tiny pinhole is a way for water to get under your roof membrane, saturate the insulation, and eventually find its way into your building.
Reason #3 – Saturated insulation
Is the roof’s insulation 5% saturated or 50% saturated?
The general rule of thumb is if a roof’s insulation is under 25% saturated, then it’s most likely worth repairing or restoring.
More than 25% saturation…it’s most likely beneficial to the building owner to remove everything and start over.
Reason #4 – Ponding water
Are there puddles of water on your roof 24 to 48 hours after a significant rain event?
If so, that’s ponding water.
This water should’ve run off your roof by then.
Ponding water can happen on a TPO roof for many reasons, such as debris and clogged drains. But if water has gotten under the TPO and saturated the insulation, making the roof sag, then that’s throwing the slope of the roof off.
This is common on TPO roofs where the slope was created using polyiso board or another type of roofing insulation. The roof’s ability to remove water is only as good as the insulation’s performance. When the performance degrades, the roof is near the end of its life.
Reason #5 – Warranty is expired (or about to expire)
A typical warranty on a TPO roof is 10 to 20 years. When it’s close to that time, a lot of these problems we talked about before start happening.
The TPO membrane wasn’t designed to last much longer than the warranty.
So, if you have a 20-year-warranty and it’s year 18 or 19, this is when you want to start thinking about doing repairs, restoring the roof, or preparing the budget to remove the entire roof and install a new roofing system.
What repair/restoration options do you have?
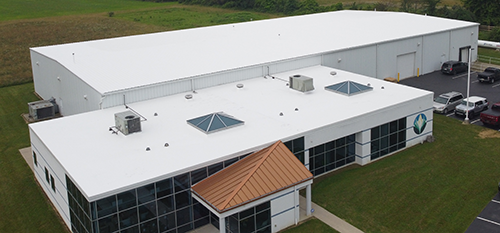
It depends on the condition of your TPO roof. If it’s in bad condition, such as the seams losing a lot of adhesion, or the majority of your insulation is wet, it’s probably beneficial to remove 100% of the roof and install a new system.
But if it’s in good condition, one great option is a silicone roof coating system.
Some may call it an SRM, a silicone restoration membrane, or simply a coating system.
These can be installed over an existing TPO roof by:
- Identifying all the wet insulation
- Removing it and replacing it with similar material
- Then prepare the existing TPO for installation by power washing and/or using a primer.
- Reinforcing the seams
- Then spraying or rolling the coating over the field of the roof
A roof coating system is a high-solid, long-lasting, paint-like material that’s been engineered to withstand weathering events.
It’s waterproof.
It expands and contracts, known as elongation. When the roof fluctuates because of temperature changes, the coating expands and contracts with the roof. A coating system does not lose any performance “moving” with the roof.
How much does each repair/restoration option cost?
(all pricing varies on product availability and material pricing)
- $10/sq. ft. for spray foam and single-ply
- $4 – $8 for SRM
- What variables for cost are there? (size of the roof, amount of wet insulation, distance away from contractor, warranty length/product used, and R-value target.)
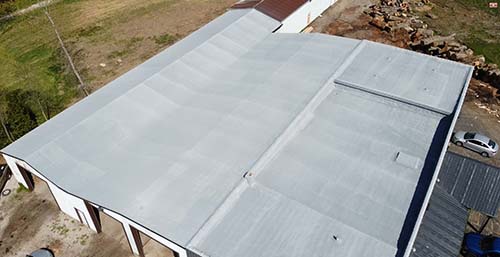
If you need to completely tear off the roof and install a new roofing system. A single-ply roof or Spray Polyurethane Foam roof is typically around $10 and up per square foot.
A metal roof would be a little bit more expensive than that.
If your roof is in good condition and you would like to restore it with a roof coating system, a typical cost is $4 – $8 per square foot.
There are a lot of variables for cost:
Variable #1 – the size of the roof
There are setup and overhead charges no matter what size a roof it is. The larger the roof, the lower per square foot the cost is going to be.
Variable #2 – the amount of wet insulation
A roof with 5% wet insulation requires far less labor than the same roof that’s 20% saturated. It’s also going to require fewer materials when replacing those areas.
Variable #3 – distance from the roofing contractor
Gas to get to your location and possible hotel stays factor into the cost of a roofing project.
The further away you are from the roofing contractor, the more expensive the project is going to cost.
Variable #4 – warranty length
A 10-year-warranty for a roof coating system requires 20 mils (in thickness) of material over the field of the roof.
A 20-year-warranty for a roof coating system requires 30 mils (in thickness) of material over the field of the roof.
The longer the warranty, the more materials that are used, and the more costly the roofing project will be.
Variable #5 – R-value target
If you’re re-roofing (installing a roof system over what you already have), then there’s no minimum R-value required by building codes.
Perhaps you’ll install 2 inches of foam in this case.
Let’s say your roof is in bad shape and it needs to be removed down to the deck before installing a new roof system.
In this case, there’s a minimum R-value requirement.
Every region is different, but in Ohio, it’s an R-25. In this case, you’d have to install about 4 inches of spray foam to get to an R-25. R-6.5 per inch of thickness, times 4, is an R-26.
If you went the single-ply route, you’d have to install enough insulation to hit an R-25. If there was no minimum R-value, you don’t need to use as many materials to get a leak-free roof.
What problems should you look out for?
The first problem you should look out for is an accurate report on the current condition of your TPO roof.
Unless you were there during the installation, how would you know if the TPO roof is 5, 15, 25, or 35 years old?
Any roofing contractors should give you evidence of pinholes, evidence of ponding water, or evidence of the TPO membrane wearing away due to normal weathering events.
They should also give you evidence of wet insulation, water entry points, and failed flashings, all these things should be pointed out to a building owner before a building owner decides on what they should do.
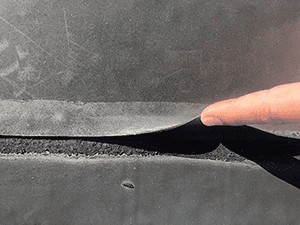
You should also get an infrared scan to identify the percentage of wet insulation. If your roof is only 5% saturated, yet a contractor proposes to remove 100% of the roof, that should be a red flag.
Unfortunately, there are good and bad roofing contractors out there.
To save yourself money, headache, and not getting ripped off, you should get a detailed reporting on the current conditions of the roof.
The report should come with photos or videos, possible recommendations, scope of work, and detailed warranty information.
Note: Another piece of advice is to get quotes from multiple roofing contractors. Get quotes from contractors installing different roofing systems. Maybe get one spray foam, one roof coating system, a metal installation, and a single-ply one. That way you can see the scope of work, the cost, the warranty length, and any other benefits that the roofing system offers you. This way you have multiple options that you could submit to your board or handle privately. This just gives you more ammo so that you can make the best decision for your roofing situation.