Quick Summary: A spray foam roofing system or a silicone roof coating system minimizes business interruption. The reason is that during the installation, tear-off can be minimized (in most cases) by going over the existing roofing system. Since they are fluid-applied, they reduce project time as they are easy to install around penetrations, such as HVAC units, skylights, and drains. Penetrations slow down the installation time for traditional roofing systems.
Suppose you came into your building this morning and saw the roof leaking.
You know that “something” has to get done.
You might ask yourself, “How will this repair interrupt normal business operations?”
In this post, we’ll cover:
- Which roofing systems minimize business interruption…and why?
- What “things” need to happen when this system is installed?
- And why other roofing systems don’t minimize interruption
And just so you’re aware, West Roofing Systems has been in commercial roofing since 1979. A primary concern (besides cost) is how the installation will affect everything else going on.
This article has been read, edited, and approved for publishing by a commercial roofing expert with more than 30 years of experience.
Let’s get started!
Which roofing systems minimize business interruption?
It’s a tie between two roofing systems:
- Spray polyurethane foam
- Roof coatings
They minimize business interruption in three ways:
- Minimizing tear-off
- Speed of installation
- Space on the job site
Let’s get into each of these below:
Minimizing tear-off
Per building code, if you have two or more roofing systems installed, you cannot install a 3rd one. You’ll have to at least remove 100% of 1 roofing system before installing a new one.
Sometimes, if the first roofing system is dry, you can keep it and just remove the top system.
Keeping one roofing system is beneficial because it saves on labor, keeps some of the remaining insulation requirements, and diverts more debris from landfills.
However, you can avoid a tear-off with roof coating systems because they aren’t technically a “roofing system.” Roof coating systems are considered maintenance. They almost always come with new 10, 15, or 20-year warranties.
While avoiding a tear-off is great for minimizing business interruption (and cost), there is a slight issue.
Roof coating systems have strict eligibility, which you can learn about in this article.
But let’s say that you only have one roofing system in place.
You only need to remove the areas with saturated insulation or damaged membrane to install a spray foam roof (or a roof coating system).
These areas are designated with an infrared inspection and/or a visual inspection.
This could be 10% of a roof.
Just remove the 10% and replace it with similar material. Properly prepare the roof (this involves different steps depending on the existing roofing system). And then install spray foam or coatings over the existing roof.
Speed of installation
Since spray foam and coating systems are fluid-applied, they can be installed quickly around penetrations. Here’s a video of spray foam being installed around an HVAC unit:
Some roofs have hundreds of penetrations, HVAC ductwork, satellite dishes, etc. Spray foam’s ease of installation reduces the installation time versus traditional roofing systems.
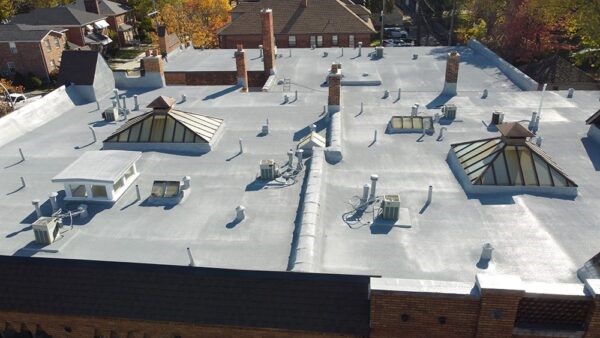
Space on the job site
For example, on a 100,000 sq. ft. roof that’s to be coated, it would only take 8 pallets of coating drums to do that job.
Versus…
A traditional roofing system which potentially needs:
- 100,000 sq. ft. of iso board, coverboard, and/or membrane
- Boxes of screws
And more.
Going over the existing roof minimizes the space in a parking lot or around a building that could displace employee parking lots, interrupting their day-to-day business operations.
What “things” need to happen when installing a spray foam or coating system?
A potential problem with spray foam and coating systems is overspray. Since it’s fluid-applied and very lightweight, it can be carried by the wind onto undesirable assets, such as employee vehicles.
However, overspray is mitigated by:
- Using windscreens
- Spraying out of a booth
- Or not spraying at all on a windy day
One “thing” that may need to happen during all spray foam installations is the covering of employee vehicles (if they are near the building). Or to have the employees park elsewhere. A supervisor will coordinate this with the customer’s representative.
This isn’t a “business interruption,” but it must occur.
Something else that may need to happen is the covering of HVAC units during the installation. With an applied product, overspray can get on the unit, which we don’t want to happen.
This could interrupt normal business operations if climate control is needed.
Why other roofing systems can’t minimize interruption
There are two reasons:
- They tend to maximize tear-off
- They can be slower to install
Maximizing tear-off
When an existing single-ply (TPO, EDPM, PVC), Metal, or Built-up roof exists, and a new single-ply, metal, etc. roof is proposed, it may require a 100% tear-off.
100% tear-off not only costs more than restoring a roof, but it takes more time to install, which increases the likelihood of interruption to your business.
NOTE: Companies are offering what’s called a “re-skin.” This is where they install a coverboard over the membrane, and then a new TPO/EPDM roof is installed.
Slower to install
Traditional roofing systems are easy to install if there aren’t many interruptions to the installation process. Traditional roofing systems are usually rolled-out sheets. The installation slows down when something gets in the way, such as an HVAC unit.
The sheet must be custom-cut when running into an HVAC unit, skylight, curb, or drain. Boots, sealants, and termination bars might have to be used. A slower installation means the contractor is on your premises longer.
Conclusion
You might be thinking, why would a building owner care about business interruption when getting their roof repaired, restored, or replaced?
Well, business interruption…interrupts business.
Sometimes a business cannot function when the roof is being repaired. For example, a resort might have to close a pool for a day or two while the roofers are nearby.
The roofing system you install can significantly affect how your business can function while it’s being repaired, restored, or replaced.
What’s next?
Here are some other resources you might find helpful:
- Case Study – Sharpsville Container – Learn how spray foam was installed over 4 different roofing systems, including steep slope metal, saving the client money.
- Case Study – Heskett Middle School – Learn how spray foam was installed 50% faster and for $1M less than a complete tear-off.
- Video – Start to Finish – Spray Foam Over a Low-Slope Metal Roof