Installing a spray foam roof is the easiest and most cost-effective way to raise low spots on a commercial roof.
There are two reasons why:
- The slope is easily manipulated by spraying more or less foam.
- You won’t have to piece together the membrane after the insulation is replaced
If you’ve never seen spray foam installed, please watch the video below:
Other commercial roofing systems, such as TPO, EPDM, and BUR, are flat. The slope of those systems is created using different heights of insulation board. This is called a “tapered system,” and it’s costly and time-consuming to create.
However, there is one issue: the roof is likely sagging due to wet insulation.
No roofing system, including spray foam, should be sprayed over wet insulation.
How to raise a low spot by installing a TPO, EPDM, or BUR roof:
- Identify and remove wet insulation
- Taper new insulation to provide adequate slope
- Fasten membrane over new insulation
- Piece together the membrane to the existing roof
How to raise a low spot by installing a spray foam roof:
- Identify and remove wet insulation
- Install new insulation with similar material
- Install spray foam at the correct thickness to achieve proper slope
The difference?
The tapered system is labor-intensive and requires more time to install. With more roofing material to piece together, there’s more room for installer error.
Spray foam is self-adhering.
This means it’ll adhere to the new insulation and to the existing membrane seamlessly.
Using spray foam to raise lower roof areas is faster, easier, and more cost-effective for a building owner.
Here’s a photo of a roof with low spots:
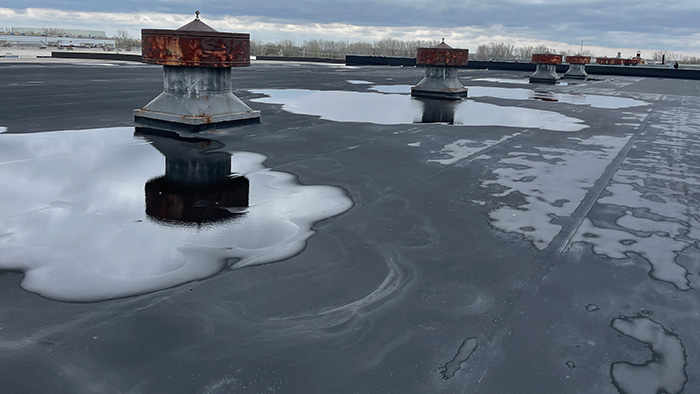
Here’s a photo of the same roof after spray foam was installed:
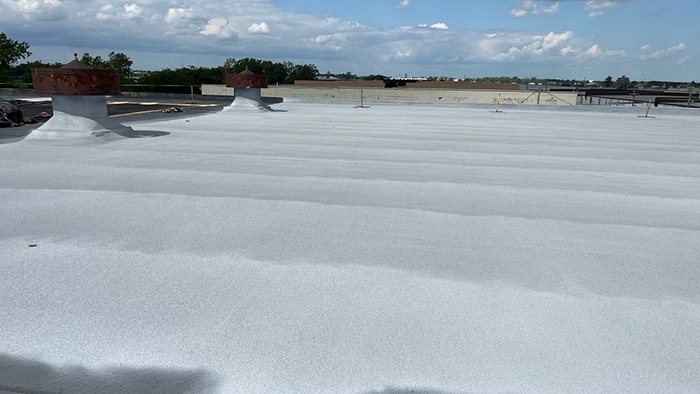
What are your next steps?
Learn some more about spray foam.
Here are some popular articles: