If you notice your roof is leaking or becoming aged, you have a few options: patch repairs, restoration, or a full roof replacement. Depending on the size of your roof, it could become costly very quickly to repair or replace your roof system. Luckily, a good contractor will offer you a few roofing solutions.
This article talks about how silicone can be used to save you money on a full commercial roof replacement.
Why Silicone is Useful for Roofing
Silicone is often used in the roofing industry because it is a reliable product that’s been proven to last a long time against weather. When compared to alternatives, such as acrylic, silicone stands up to sun and severe weather without cracking. Silicone can also hold standing water for long periods of time without degrading or leaking.
Silicone has many characteristics that make it useful on commercial roofs:
- Thoroughly coats the existing roof material
- Choice of thickness
- Prevents rust
- Reflects UV rays
- Waterproof
- Eco-Friendly
- Cost-effective
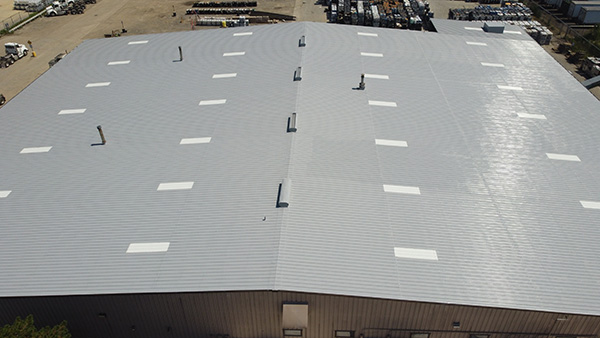
How to Use Silicone for Roof Repairs
When you have a roof that’s leaking, it may not be in your best interest to have a contractor use silicone sealants to patch individual leaks. That process can be time-consuming, and there’s a higher risk of leaking areas being missed. We often recommend that buildings with a stable roofing system go through the roof restoration process.
Silicone can be used to create a silicone restoration membrane on almost any existing roof system. By applying a layer of silicone across the entire roof, you can eliminate leaks and form a waterproof membrane across the entire current roof system.
There are many benefits to choosing a silicone restoration membrane:
- Cost Savings – As long as the existing roof substrate is dry and stable, no roof removal is required, saving you money on labor and materials.
- Extended Roof Life – If your roof is in relatively good condition, you can extend the life of your commercial roof by protecting it from the elements.
- Reduced Energy Expenses – Silicone roof coatings are often referred to as “cool roofs” due to their ability to keep facilities cool. The bright white color reflects UV rays, saving buildings up to 35% in energy.
- Short Project Duration – Silicone coating projects can cut down project duration up to 30%.
Silicone Restoration Membrane Installation
A Silicone Restoration Membrane (SRM) is a fluid applied silicone coating sprayed directly onto an existing roof system.
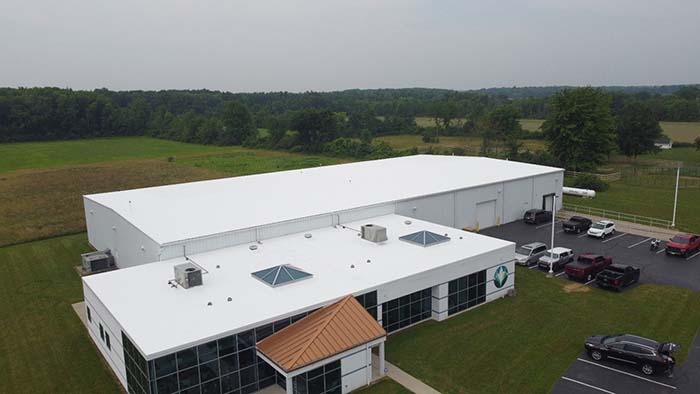
The process of installing a silicone restoration membrane is relatively straightforward:
- An infrared inspection is performed to see if there are any wet areas of insulation under the membrane.
- After any wet areas have been removed and replaced, the entire roof surface is power washed clean to remove any contaminants.
- The seams of the membrane are then reinforced with a self-adhesive tape or mesh and coating.
- The silicone coating is sprayed on or roller applied over the entire surface of the roof, creating a seamless membrane.
- After the silicone coating membrane has been completed, a final inspection will be performed by a third-party or the manufacturer’s representative to verify all the necessary repairs were performed properly and the silicone is applied accurately. When the repairs and silicone membrane coating are approved, the warranty is issued.
Silicone Restoration Membrane Success Story
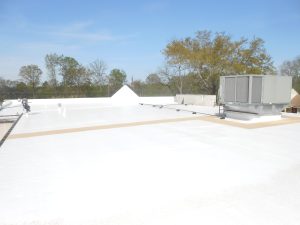
We had a customer interested in replacing their existing Single-Ply EPDM Membrane roof system with a new EPDM Membrane. While we provided a proposal for the replacement of the existing EPDM roof system, we also gave them an option to apply a Silicone Restoration Membrane (SRM).
The cost of the SRM was 45% of the cost of the full replacement. Additionally, we were able to provide a 15-year full system manufacturer’s warranty and cut down the project time by 30%.
It was a very easy decision on their owner’s part for the SRM installation instead of a roof replacement.
Read More: Gorilla Glue Case Study: Reviving the 25 Acre Roof
Read More: