A metal roof can be an excellent option for your commercial building because of its durability, the variety of designs available, and cost-effectiveness. But that metal roof can go through wear and tear leading to problems for your facility.
With proper maintenance, your metal roof system can last a long time. And with a timely metal roof restoration, you can save a lot of money and prolong the life of your roof.
In this article, we will cover:
- The basics of commercial metal roofing
- The problems metal roofs have
- How you can restore your metal roof
- If your metal roof is eligible to be coated
- The six steps on how a contractor would coat a metal roof
- And the benefits of a newly restored metal roof system
About Commercial Metal Roofing
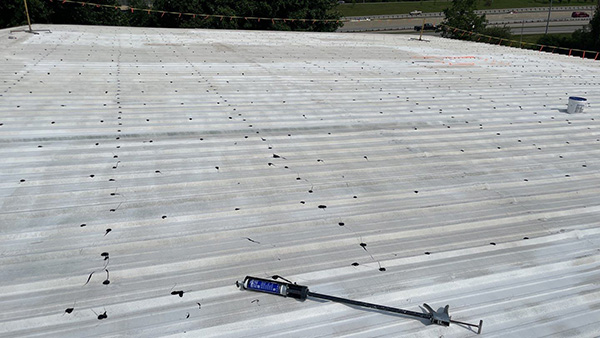
Metal Roofing is one of the oldest commercial roofing systems on the market. Most metal roofing systems use corrugated galvanized steel, although other materials such as aluminum or tin can also be used. After a metal roofing system is installed, a coating can be added for waterproofing, rust protection, and UV protection.
For an average commercial roof, it will usually cost at least $10.00 per square foot in materials and labor to install a typical metal roofing system. This price range can change depending on the type and style of the metal panels you choose.
There are a few types of insulation options available:
- Roofing Felt
- Fiberglass
- Rigid Board
- Bubble Insulation
- Spray Foam
Metal Roofing Problems
While metal roofing systems can have a long lifespan, this can only be obtained if the roof is adequately maintained over the years. This includes a coating to avoid rust and proactively replacing and re-fastening damaged panels.
Here are other problems you can face with metal roofing systems:
- Water Damage – If water ponds on the roof it can cause severe damage, such as rust.
- Full Replacement – The substrate, or frame, is often cumbersome and difficult to work with. They require a complete tear-off in almost every replacement instance.
- Seams – The metal panels create seams that are prone to water leaks.
- Durability – Since the metal panels are attached to the substrate, if they are not installed correctly, they can become loose when they expand and contract.
- Noise – Weather such as rain, hail, or wind can create a lot of noise against the metal material.
Is Your Commercial Metal Roof Eligible for Restoration?
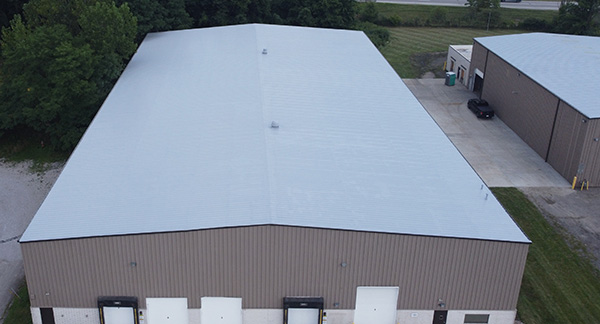
With any commercial roof restoration, eligibility is determined by the condition of the existing roof system. If your existing metal roof is severely damaged, then restoration may not help your problems or even be possible.
The best way to find out if your facility is eligible for a roof coating system is to schedule a contractor to evaluate your existing roof system. They will be able to recommend the best solution for your facility’s needs.
For an existing roof system to be eligible for a roof restoration, the roof needs to be in better condition than most roofs at the end of their serviceable life. Some signs of a roof in good condition include:
- The seams of the existing membrane are relatively intact
- The field of the roof has been adequately maintained over its life
- Less than 25% of the underlined substrate and insulation is wet (It is still cost-effective to do spot replacement of small saturated areas rather than a complete replacement.)
How to Restore a Metal Roof
A silicone roof coating system is a coating applied directly onto an existing roof. The silicone can be sprayed or roller-applied right onto your metal roof system.
The process of installing a silicone roof coating system is straightforward:
Step 1: Inspection
Before you can begin restoring a commercial metal roof, you need to inspect it thoroughly to identify any areas that require repair or replacement. Start by examining the roof from the ground to identify any visible damage, such as dents, rust, or loose panels. Then, climb onto the roof and conduct a more detailed inspection. Look for signs of corrosion, cracks, and leaks, paying particular attention to areas around vents, skylights, seams, and other roof penetrations.
Step 2: Cleaning
The next step in restoring a commercial metal roof is to clean it thoroughly. Over time, dirt, debris, and other contaminants can build up on the roof, which can cause damage and reduce its lifespan. Begin by sweeping the roof to remove any loose debris. Then, use a pressure washer to clean the roof, not damaging any of the panels. If there are any areas of particularly stubborn dirt or grime, you may need to use a specialized cleaner.
Step 3: Repair
Once the roof is clean, it’s time to start repairing any damage. Begin by replacing any damaged or missing panels. If the damage is more extensive, you may need to replace entire sections of the roof. Check all of the fasteners to make sure they are secure, and replace any that are loose or damaged. If there are any leaks, repair them using a suitable sealant. Any wet insulation will need to be removed and replaced.
Step 4: Seam Reinforcement
Seams are the most prone to roof leaks, so reinforcing them is important. A contractor will install a thin layer of coating, then install a “mesh”, and then install more coating over the mesh.
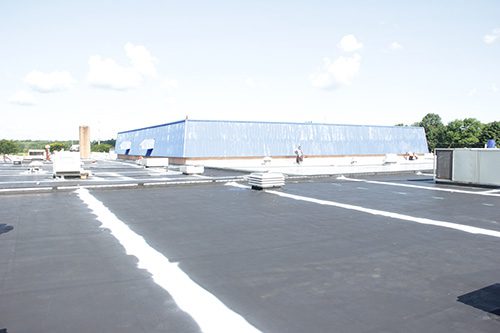
NOTE: this is seam reinforcement on a rubber roof, but it’s same technique that’s used on a metal roof.
Step 5: Coating
Once the repairs are complete, it’s time to apply a coating to the roof. The coating serves as a protective barrier, helping to prevent damage from UV rays, weather, and other environmental factors. There are a variety of different coatings available, including acrylic, silicone, and polyurethane coatings. Be sure to choose a coating that is appropriate for your particular type of metal roof.
Step 6: Inspection and warranty granted
Once the installation is complete, in some cases a third party will inspect the roof. They will check the integrity of the installation, as well as the thickness of the installed coating.
If you’re unaware, the warranty length is determined by the thickness of the coating.
For example:
- a 10-year-warranty gets 20 mils of coating
- a 15-year warranty gets 25 mils of coating
- a 20-year-warranty gets 30 mils of coating
If the coating is too thin, the contractor will install more coating.
If your commercial flat roof is in good working condition, you can install a silicone roof coating system to extend the life of your roof and renew your warranty. But how much does it cost?
For an average 20,000 sq. foot commercial roof, it will usually cost between $4 and $8 per square foot in materials and labor to install a typical silicone roof coating system.
Benefits of a Metal Roof Restoration
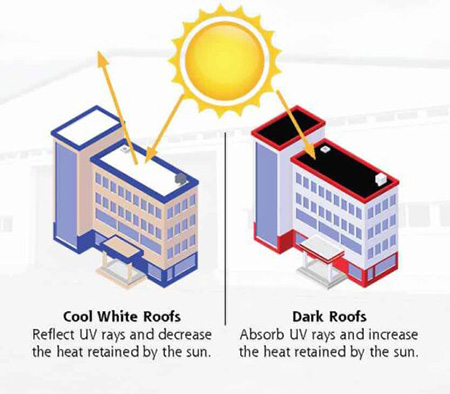
A silicone roof coating system can save your business money on time, material and labor costs. In addition to the cost-savings, there are a few other cool benefits to a metal roof restoration:
Cool Roof Savings
Silicone roof coatings are often referred to as “cool roofs” due to their ability to keep facilities cool. The bright white color reflects UV rays, saving buildings up to 35% in energy costs from not needing as much air conditioning to keep the facilities cool. Utilizing a bright white coating application reduces energy costs as part of the energy star cool roof solution.
New Warranty
A silicone roof coating system, when installed correctly by a reputable contractor, comes with a warranty that can cover up to 20 years.
Renewed Protection
The silicone roof coating system will add a new waterproof layer to your metal roof system. When properly maintained, this layer will prevent leaks into your building and protect your metal system from UV rays.
Read More: Gorilla Glue Case Study: Reviving the 25-Acre Roof
Silicone roof coating systems are an eco-friendly, cost-effective, alternative to replacing your commercial roofing facility.