When it comes to commercial roofing, making the right decision can save building and property owners thousands of dollars and countless headaches.
Here’s a comprehensive guide to help you navigate the world of commercial roofing, from understanding different roofing systems and their costs to identifying common problems and exploring innovative solutions like roof coating systems.
Here’s what’s covered in this article:
- Overview of the most popular commercial roofing systems
- Ballpark costs of commercial roofing systems
- Common problems that happen in commercial roofing
- Based on your existing roof, what options do you have if there are issues?
- Why are big box retailers installing roof coating systems?
Just so you know, West Roofing Systems has been in commercial roofing since 1979. We’ve seen every roofing system out there, including ones that have become extinct, ones with formulation changes that are more environmentally friendly, and so on.
We want to provide building owners and property managers with all the information they need to make the best decisions about their roofs.
One of our owners, who has been in commercial roofing for 30+ years, has read, edited, and approved this article for publication.
Let’s get started!
Overview of The Most Popular Commercial Roofing Systems
- Metal Roofing: These systems offer superior durability (often lasting 40+ years) and can be made from various metals, including aluminum, steel, and copper. They are resistant to fire, wind, and impact but can be prone to rust and corrosion if not correctly maintained.
- TPO Roofing: TPO roofs are popular for their reflectivity. They are flexible and can accommodate building movements without cracking or tearing.
- EPDM Roofing: EPDM is a synthetic rubber membrane that performs well in various climates. They are also flexible and can accommodate building movements without cracking or tearing.
- Spray Polyurethane Foam Roofing: SPF roofs offer the best R-value per inch of thickness versus any roofing insulation. It’s a seamless application that prevents leaks. They are lightweight and can be applied over most roof types, making them versatile. Their warranties are renewable, making future roofing costs easy to forecast.
- Roof Coating Systems are applied as a liquid coating that cures into a seamless membrane. They are highly reflective, reducing energy costs and extending the life of the existing roof. The coating is sacrificial, naturally wearing away over time. Once the coating wears thin, the roof needs to be correctly prepared, and then a recoat can happen, which grants the building owner a new warranty. The “recoat/new warranty” process can be repeated indefinitely.
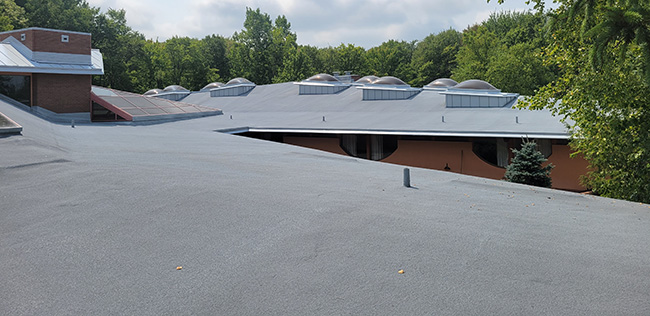
Ballpark Costs of Commercial Roofing Systems
- Metal Roofing: Metal roofs cost from $15 to $25 per square foot, depending on the type of metal and complexity of the installation.
- TPO: TPO costs typically range from $5 to $10 per square foot, depending on the thickness of the TPO and how much insulation is installed.
- EPDM: EPDM generally costs between $5 and $10 per square foot. Same variables with cost as TPO.
- SPF (Spray Polyurethane Foam): costs ranging from $5 to $10 per square foot. The thickness of the material, existing roof conditions, and length of warranty greatly influence the cost. Many variables can influence cost.
- Roof Coating System: costs typically range from $3 to $7 per square foot. Cost is greatly influenced by the thickness of coating and the severity of roof preparation. Many variables influence the cost of roof coating systems.
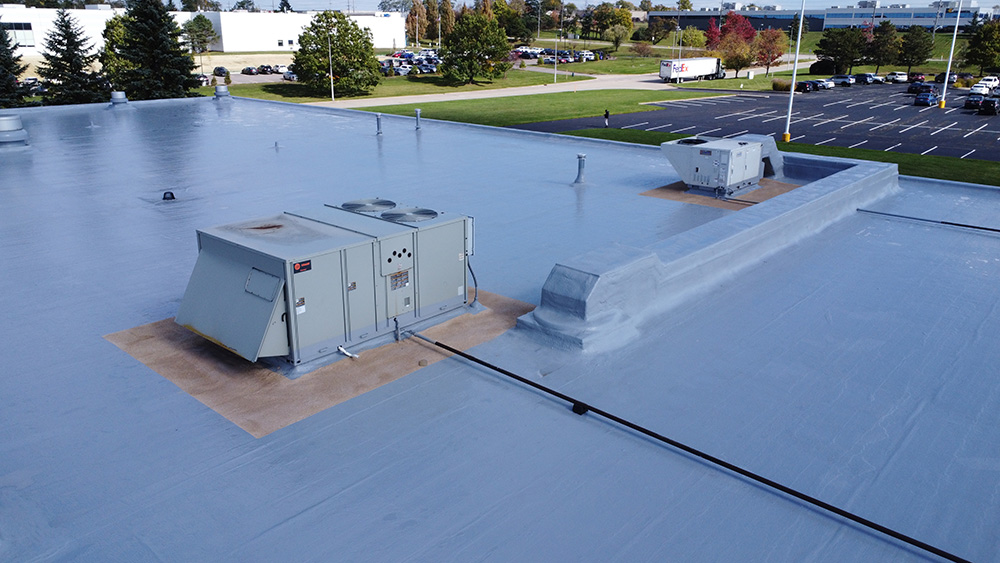
Common Problems in Commercial Roofing
- Bad Contractors: Poor workmanship can lead to many problems, including leaks, premature roof failure, and voided warranties. It’s essential to hire experienced and reputable contractors. This means paying for a more experienced roofer, even if they aren’t in the area. A common problem that happens is two companies are similar, yet one is cheaper simply because they are closer to the job site than the competitor. The building owner doesn’t consider experience or professionalism, and they get an inferior installation.
- Installing Over Wet Insulation: Moisture trapped under the roofing material can lead to mold growth, decreased insulation efficiency, and structural damage. Proper inspection and moisture detection are crucial before installation. Some “shady” contractors will avoid identifying, removing, and replacing wet insulation before an installation. They do this to keep costs down and win bids. However, this is unethical. The contractor knows bad things will happen to the roof when they install materials over wet insulation.
- Not Eligible for a Coating System: Building owners see the cost range for coating ($3 – $7 per sq. ft.), know it’s likely the cheapest option, and will want to go with it. However, there are strict eligibility requirements needed to get a warranty; they are:
- Maintenance: The roof must have been maintained annually, and minor repairs have been addressed promptly
- Insulation: At least 75% of the roof’s insulation is dry
- Seams: If the roof has seams, the adhesion between them must be in good condition
If any of these conditions aren’t met, no contractor or manufacturer will grant a warranty.
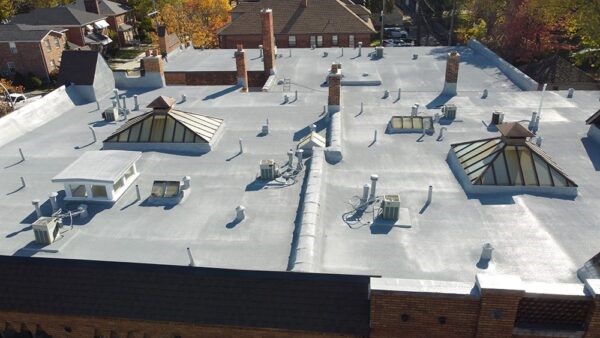
Options Based on Existing Roof Types
- If you have a metal roof, consider metal roof restoration, such as adding a coating system or installing spray foam over the existing roof. Or replace sections with new metal panels.
- If you have a TPO roof, options include patching damaged areas, applying a TPO-compatible roof coating system, or full replacement.
- If you have an EPDM roof, you might opt for repairs, an EPDM-compatible roof coating system, or overlaying with a new membrane.
- If you have an SPF roof, regular maintenance and re-coating can extend its life. Or consider scarifying the existing foam, removing all debris, and installing new foam and coating.
- If you have an SRM roof, periodic re-coating and annual maintenance can keep it in top condition. It’s worth noting that if you have a silicone roof coating system, nothing will stick to silicone…besides more silicone.
Why Big Box Retailers are Installing Roof Coating Systems
Big box retailers are increasingly turning to roof coating systems for several reasons:
- Cost-Effectiveness: Coating systems are more affordable than complete roof replacements.
- Renewable Warranties/Better Forecasting – When the coating reaches its lifespan (usually 10-20 years) a contractor can prepare the roof, install a new coating thickness, and grant a new warranty. The process can be repeated. This makes forecasting future roofing costs more predictable.
- Energy Efficiency: Reflective coatings reduce cooling costs by reflecting sunlight and reducing heat absorption. They also reduce the burden on HVAC units, making them more efficient and not working as hard to maintain a comfortable temperature inside the store.
- Minimal Disruption: Applying a coating system is less disruptive to daily operations than tearing off and replacing a roof.
- Sustainability: Coating systems extend the life of the existing roof, eliminating the complete tear-off and reducing landfill contributions.
In conclusion, understanding the various commercial roofing systems, their costs, benefits, and potential issues can help you make an informed decision. Whether you’re dealing with a metal, TPO, EPDM, SPF, or SRM roof, knowing your options and the advantages of roof coating systems can lead to better long-term outcomes for your property.