Quick Summary: The ballpark cost to restore an EPDM roof is $3.50 -$7 per square foot. The ballpark cost to restore a TPO roof is $4 -$7 per square foot.
So, you have a TPO or EPDM commercial roofing system and you need it fixed. Maybe it’s leaking, old, or out of warranty.
You already know the least cost-effective option is to completely tear off the roof and start over (although sometimes that might be your only option.)
So, what about restoration? And what about using silicone roof coating systems?
In this article, you’ll learn:
- The ballpark cost of a roof coating system over an existing TPO roof
- The ballpark cost of a roof coating system over an existing EPDM roof
- The 11 factors that influence the cost of a roof coating project
This article has been read, edited, and approved for publishing by one of our owners, who has over 15 years of roof coating experience (since they were invented) and over 30 years of commercial roofing experience.
Let’s get started!
- The ballpark cost of a roof coating system over an existing TPO roof is $4 – $7 per square foot
- The ballpark cost of a roof coating system over an existing EPDM roof is $3.50 – $7 per square foot.
What factors make the cost go more towards $4…..or $7?
- Amount of wet insulation or decking removed and replaced
- New flashings, gutters, downspouts, or metal drip edge
- New breather (or one-way) vents
- Cleaning solution required?
- Adhesion promoting primer
- Bleed blocking primer
- More coating/longer warranty
- Eliminating standing water
- Distance from the roofing contractor
- Fasteners added for increased attachment
- Vendor costs for silicone
We explain each of these points below:
Amount of wet insulation or wood decking removed and replaced
No roofing system should be installed over wet insulation or deteriorating decking. Not fixing these will cause long-term issues with your roof.
These areas are identified with a visual inspection, pulling core samples, and thermal imaging.
A roof where 10% of the decking is bad and 20% of the insulation is wet; this roofing project will cost more than a project with no decking or insulation issues.
Amount of metalwork added to a project
New flashings, gutters, downspouts, and/or metal drip edges are included in some scopes of work. These will all add to a project’s cost.
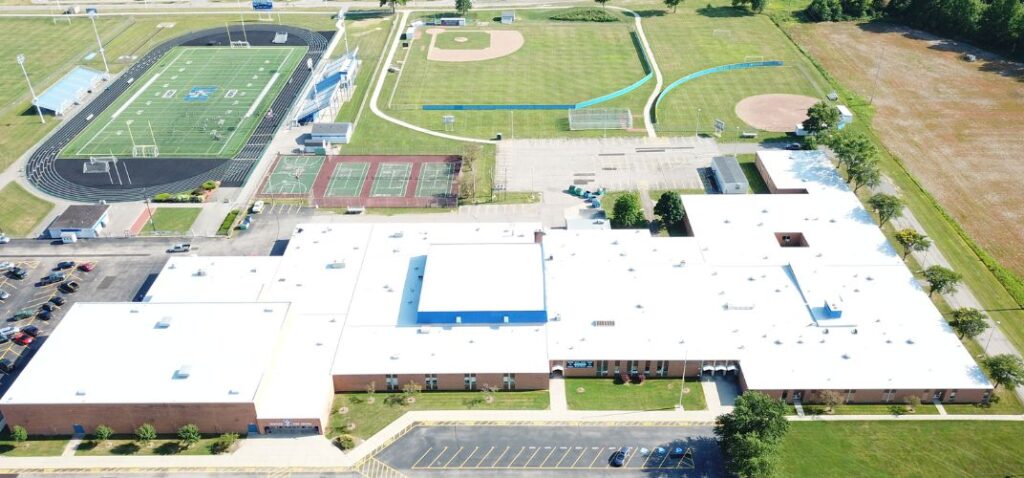
New breather (or one-way) vents
Sometimes, when a core sample is pulled, there’s a presence of moisture. The insulation is damp, not soaked, so it doesn’t need to be removed and replaced. But moisture cannot be trapped. The addition of breather vents will take care of this issue.
Cleaning solution
Does the manufacturer require a cleaner to be used during the pressure washing phase? If so, are there local requirements for capturing the runoff of the water/cleaning solution? An adhesion test prior to the start of the project will tell you if a cleaner is necessary, and if so, will increase the cost of the project.
Adhesion promoting primer
Adhesion tests are always performed before a coating system is installed. If the adhesion fails the manufacturer’s adhesion test guidelines, a primer is needed to meet their threshold.
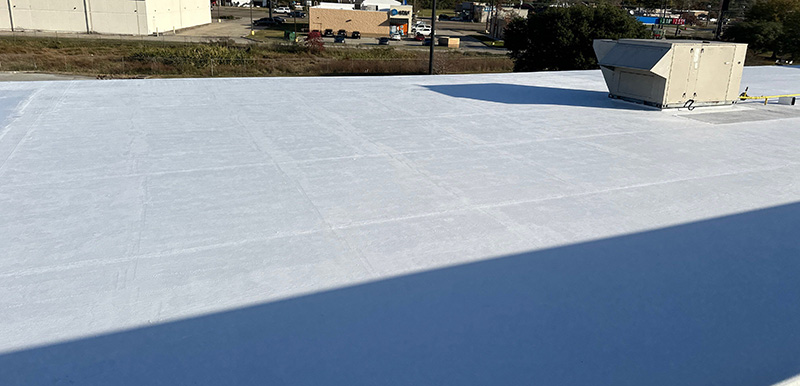
Bleed blocking primer
When you add a white/grey colored silicone coating onto an asphalt-based roof, some of the oils in the asphalt will bleed through the coating.
This will turn a white-coated roof more yellow. The yellow doesn’t affect performance. It’s more of an aesthetics thing. The bleed blocker primer will prevent this from happening
More coating/longer warranty
Most roof coating systems come in 10-20-year warranties.
- For a 10-year warranty, a total 20-mil thickness of coating will be installed in two separate coats
- For a 15-year warranty, a total 25-mil thickness of coating will be installed in two separate coats
- For a 20-year warranty, a total 30-mil thickness of coating will be installed in two separate coats
The more coating that’s installed, the more the project will cost.
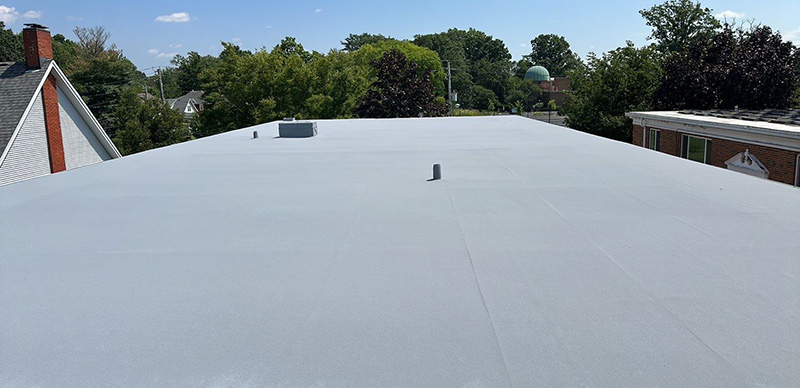
Eliminating standing water
Some roofs have issues with “standing” water, AKA water that will not run off the roof or towards drains in adequate time.
Some roofs have areas that have sagged over time. This causes issues with the slope the roof was initially designed to work with. These areas need to be “built up” to restore the proper slope.
Building up a roof can be done with spray foam. It can also be done by tapering insulation or using a recovery board.
Distance from the roofing contractor
It’s no magic that gas, labor hours driving, and hotel stays influence the cost of a roofing project. The closer you are to the contractor, the less travel costs will be injected into the price.
However, picking a roofing contractor based solely on location is a terrible idea.
The quality of the installation is the most important aspect of any roofing project. Whichever company gives you the most confidence that a quality install will happen, is the one you should choose.
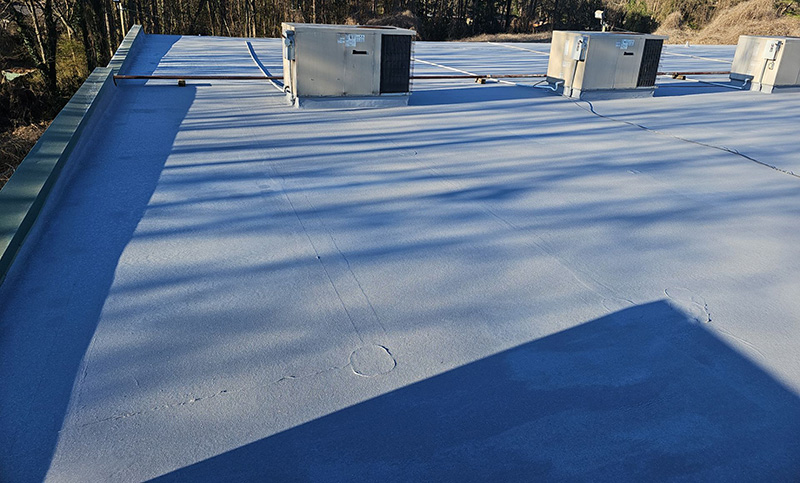
Additional fasteners added for increased attachment
A roof coating system is reliant on the membrane below. If the existing membrane isn’t properly attached to the insulation or deck below, the coating will mirror what the membrane does.
Vendor costs for silicone
Roofing contractors are reliant on silicone coating manufacturers for products. The prices for silicone constantly change. Changes in the economy fluctuate the price. Labor shortages and raw materials influence the price.
Sometimes a quote for a roofing project is only good for a week. This is because the coating price can be much higher one week from today.
Conclusion
Hopefully, this will give you more insight into the cost of silicone roof coating projects for TPO and EPDM roofing systems.
The more preparation that’s needed, the more likely the project will cost.