When you get a quote for a commercial roofing project, it’s important to understand how the costs break down between materials and labor. This knowledge can help you make more informed decisions about your investment.
It’s not out worldly for a commercial roofing project that’s installing a traditional roofing system (TPO, EPDM, Metal) to be 60% labor and 40% material cost.
Spray foam roofing systems typically are reverse. 60% of the costs go towards the materials used on the project…which is a good thing!
Before you get any further, I wanted to let you know that West Roofing Systems has been in commercial roofing since 1979.
One of our owners, with more than 30 years of commercial roofing experience, has read, edited, and approved this article for publication.
Let’s get started:
Long-term Investment: Materials vs. Labor
The key to a cost-effective roofing project is maximizing the percentage of your budget spent on materials rather than labor. Roofing materials stay on the roof every day and night for decades, providing ongoing protection, R-value, etc.
In contrast, labor costs are temporary, with workers completing their tasks and leaving the site once the project is complete.
TPO Roofing System
Thermoplastic Olefin (TPO) roofing is a very popular commercial roofing system. TPO comes in large rolls that are mechanically fastened or adhered to the roof. However, installing TPO around roof penetrations such as skylights, vents, and HVAC units can be challenging and time-consuming. These detailed areas require skilled labor to ensure proper sealing, increasing labor costs and the overall project duration.
Spray Foam Roofing System
Spray Polyurethane Foam (SPF) offers a different approach that can significantly reduce labor time and costs. Spray foam is sprayed onto the roof, expanding into a seamless, insulating layer that adheres to any surface. This method is particularly advantageous for roofs with numerous penetrations or irregular shapes, as the foam easily conforms to these features, eliminating the need for labor-intensive cutting and fitting.
Take a look at this roof:
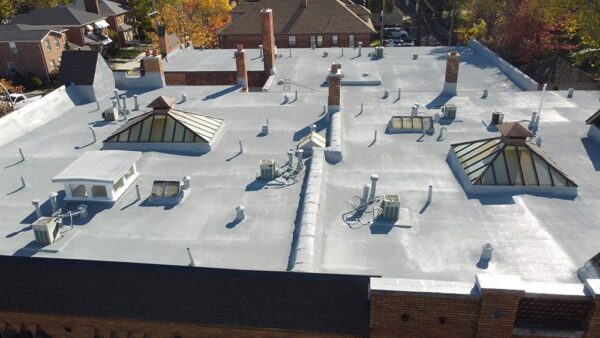
How much longer would it take to install a TPO system on this roof versus spray foam?
Much longer.
To do this roof with TPO, the labor costs would be higher than the actual materials. For a spray foam roof, the opposite would be true. The materials costs would outweigh labor. This is a good thing because most of your money is “working” on your roof after the project has been installed.
Speed and Efficiency: Spray Foam Installation
To illustrate the efficiency of spray foam, consider the process of installing it around roof penetrations. In the accompanying video, you’ll see how the foam is sprayed directly onto and around penetrations, creating a seamless and watertight seal much faster than TPO installation:
Case Study: Maryland Court – A Difficult Project Made Easier with Spray Foam
Maryland Court is a multi-surface, multi-level roof with many penetrations:
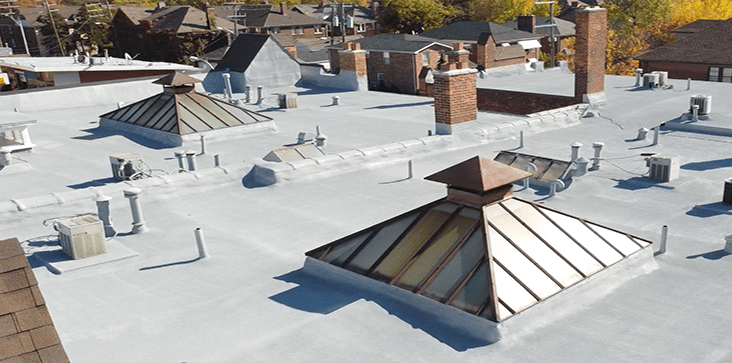
Maryland Court’s roof has irregular roof surfaces with penetrations and skylights. Initially, the project was estimated using TPO.
The TPO quote was too high, and this was largely due to the high labor costs due to the complexity of the installation.
You probably couldn’t roll TPO out more than 10 feet without having to cut it. 5 more feet and cut again.
Switching to spray polyurethane foam greatly reduced both install time and labor costs. The foam was applied directly over the existing roof surface, seamlessly integrating with the irregular features and providing excellent insulation and waterproofing.
Being “fluid-applied” sped up the installation process and reduced the labor hours, ultimately lowering the total project cost.
Here’s a link to the case study of the Maryland Court Project. The case study includes:
- Background
- Scope of work
- Materials used
- Before/after photos
Conclusion: Choosing the Right Roofing System
When comparing commercial roofing systems, it’s essential to consider both material and labor costs. TPO is a robust option but can become labor-intensive and costly, especially for complex roofs. In contrast, spray foam offers a faster, more cost-effective solution, particularly for roofs with many penetrations or irregular shapes.
The choice between TPO and SPF will depend on the specific requirements of your project.
Building owners can make more informed decisions by understanding these differences and considering the long-term implications of material and labor costs.